Flat Ass Rules of Technical Training
Before Covid lockdowns, before zoom calls, before zoom fatigue, remote learning, remote meetings, remote workplaces, virtual chats, virtual firesides, and virtual happy hours, before our lives became compressed and squeezed through little fiber optic cables and broadcast to subscribers and stuffed into virtual waiting rooms—before all that—Prime Power wondered how we could help technicians get better at their craft by leveraging the internet.
We ended up creating a first-of-its kind, best-in-industry online learning system to prepare students to become generator technicians and specifically help them prepare for EGSA certification.
To get there, we wondered what would be required. What must we do, and what must we avoid doing. What are the flat-ass rules of online technical training?
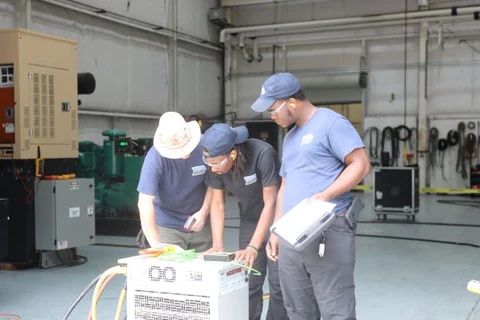
Rule 1: Technical training must be hands-on. Online learning is no substitute.
It may sound odd that the first rule on this list is that technical training must be hands-on, but before we got started, we confessed that nothing we created in the virtual environment could ever take the place of a few good hours of lab-based, hands-on training. With this in mind, we committed to build a comprehensive learning experience that included an online component. But the online addition would only supplement hands-on training, not substitute for it.
Rule 2: Technical training must be interesting.
There's nothing worse than boring, abstract lessons about real-world, hands-on topics. Unfortunately, there is a lot of online training that is just boring. Tons of companies try to pass off "voice over PowerPoint" as online learning. It's the worst, and we were very aware of it when we took on this challenge. We decided that the only way to develop high-level and interesting online technical training was to create a dynamic and interactive program that engages learners the way they already engage the internet. Our lessons are chock full of videos, pictures, knowledge checks and interactive images. The lessons are short—snackable—easy to take with you and available in your pocket. You can complete a module while waiting for the bus.
Rule 3: Technical training is troubleshooting.
Let's face it. Most training programs teach you how to change parts. Somewhere along the way, people thought that technicians didn't know how to think, or that they didn't need to. All they expected of their technicians was for them to swap out a bad part for a good part. But experienced technicians know that's not how it works. To be a good technician, you have to think with the machine you're working on. You have to understand how it works in order to determine why it broke. We train thinking technicians. We train troubleshooting.
These three rules guide our work to help you become a better technician. Give it a try and let us know what you think. We're excited to offer you something useful and engaging that will add to your experience and lab-based training to help you become a thinking technician.
Adam Mathes, PhD, President of Prime Power Services, Inc.
Learn More
- In-person training at the Roger Bisher Training Center
- Online Training
- EGSA Prep
- Technician School
- Apprenticeships
- Emergency Power Systems for Operators (online)